Side CAR-Ts
07.03.2018
Big pharma’s interest in chimeric antigen receptor (CAR)-T therapies is clear: companies such as Novartis and Pfizer have been making large investments in this field for several years, whilst others such as Gilead have spent many billions of dollars in the area in only the last six months. But the CAR-T space is very different from the small molecule world in which many of these companies have historically lived: a significant proportion of the investment has had to be not just in the underlying science, but in collaborating with those working in side industries relating to the manufacturing process and facilities, and investing in the supply chain infrastructure necessary for these therapies.
This is because these therapies cannot just be mass-produced in one self-contained process and given to a patient out of a box. Instead, in the case of autologous CAR-T therapies a multi-step, multi-location process is involved. First, a patient’s blood is collected and lymphocytes extracted from it (this usually happens at the hospital). The timing of taking the cells is co-ordinated with the rest of the patient’s treatment regimen in order to ensure that sufficient numbers of T cells are present. Next the cells are shipped to a specialist manufacturing facility. The cells may then be further processed, then the T cells activated. Next DNA encoding the CAR construct is transduced into the T cells using, for example lentiviral vectors (see below) resulting in CARs being produced on the surface of a patient’s T-cells. After this, the newly engineered CAR-T cells are grown in order to generate a therapeutic amount of the cells. Finally, the cells are shipped back to the hospital to be infused into the patient. When re-introduced into the patient’s body, these genetically engineered CAR-T cells are what targets and destroys tumour cells.
To date two CAR-T therapies have received FDA approval and are on the market in the US: Kymriah (Novartis) and Yescarta (Kite/Gilead). No CAR-T therapies have yet been approved in Europe, but this is in the pipeline as applications for approval of both Kymriah and Yescarta have been made to the EMA and accelerated review status granted. However, without the necessary supply chain infrastructure and manufacturing facilities, it would not be practical to bring these complex therapies to market (whether in the US, Europe or elsewhere), let alone possible to satisfy the regulatory requirements. For example, in Europe, as CAR-T therapies are advanced therapy medicinal products (ATMP) they will be required to comply with Regulation (EC) 1394/2007[1] (amending Directive 2001/83/EC and Regulation (EC) No 726/2004), which lays down the specific rules regarding the authorisation, supervision and pharmacovigilance of ATMPs. As with any medicinal product that has a marketing authorisation, good manufacturing practice (GMP) compliance is also mandatory, and from 22 May 2018 ATMP manufacturers should comply with the new ATMP GMP guidelines[2]. Additionally, as “blood components”[3] CAR-T therapies will have to meet the requirements regarding the standards of quality and safety for the collection, testing, processing, storage and distribution set out in Directive 2002/98/EC[4].
Investment is continuing apace in order to improve operational efficiency, reduce variability and bring down the cost of CAR-T therapies. In this article, we highlight three notable but very different companies working in collaboration with others in the CAR-T space.
Cryoport Inc. is a cold chain logistics provider that has been engaged by both Novartis and Gilead in the US to provide support for their Kymriah and Yescarta treatments respectively. Once T-cells have been taken from a patient in a hospital, Cryoport will ship these to the manufacturing facility where they are genetically engineered and then back to the hospital to be re-infused into the patient. Specialist logistics providers are needed for this shipping as not only is it of paramount importance that the right cells are returned to the right patient, but for regulatory compliance, the cells must be kept in the correct conditions in transit and monitored throughout (for example, it is not acceptable for contact to be lost with the shipments because the mobile signal drops out periodically), and this must all be done on a strict timeline. Also, patients are often so unwell that there may be no second chance if the process goes wrong.
Oxford BioMedica is a UK based company which has collaborated with Novartis since 2013 and manufactures lentiviral vectors. Lentiviral vectors are essential to Novartis’ Kymriah CAR-T therapy as they serve as the gene transfer tool. In July 2017, Oxford BioMedica entered into a new agreement with Novartis to deliver commercial and clinical supplies of lentiviral vectors which are used to generate Kymriah and other pipeline CAR-T therapies, building on an agreement from 2014 which also included licences to relevant patents in Oxford BioMedica’s portfolio. This deal could be worth in excess of $100 million to Oxford BioMedica over the next three years.
GE Healthcare The development of technology which helps companies to semi-automate and standardise biopharmaceutical manufacturing processes for industrial-scale manufacturing is not a new concept per se, but GE Healthcare has recently developed its biomanufacturing platform for the cell therapy market. It also markets individual machinery which can be used to automate key steps in cell processing, as well as staff training and digital solutions. Indeed, an increase in automation is seen as a way to increase efficiency and minimise the chance of contamination. In January 2018, GE Healthcare announced a collaboration in this space with Cellular Biomedicine Group Inc (CBMG), a clinical-stage Chinese biopharmaceutical company engaged in the development of CAR-T therapies. CBMG will configure part of its facility in Shanghai with GE Healthcare’s platform and work together with GE Healthcare to develop an integrated and automated CAR-T cell preparation system. With the current list prices of Kymriah and Yescarta at $475,000 and $373,000 respectively, any technology which can simplify and bring down the cost of the complex and highly regulated manufacturing process will be welcomed by the healthcare industry and payers alike.
[1] https://ec.europa.eu/health//sites/health/files/files/eudralex/vol-1/reg_2007_1394/reg_2007_1394_en.pdf
[2] https://ec.europa.eu/health/sites/health/files/files/eudralex/vol-4/2017_11_22_guidelines_gmp_for_atmps.pdf
[3] Article 3 of Directive 2002/98/EC
[4] http://eur-lex.europa.eu/LexUriServ/LexUriServ.do?uri=OJ:L:2003:033:0030:0040:EN:PDF
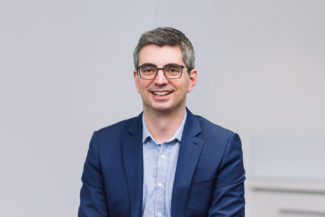
Gregory Bacon
Author
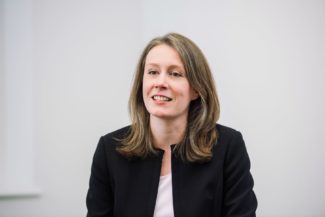
Rachel Mumby
Author